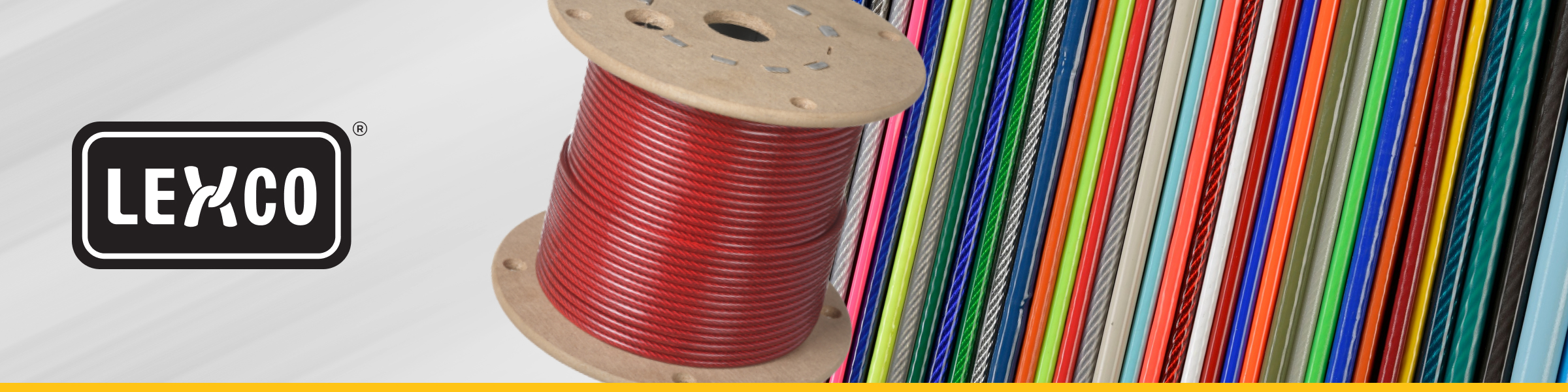
HOW AND WHY AIRCRAFT CABLE AND WIRE ROPE ARE EXTRUSION COATED
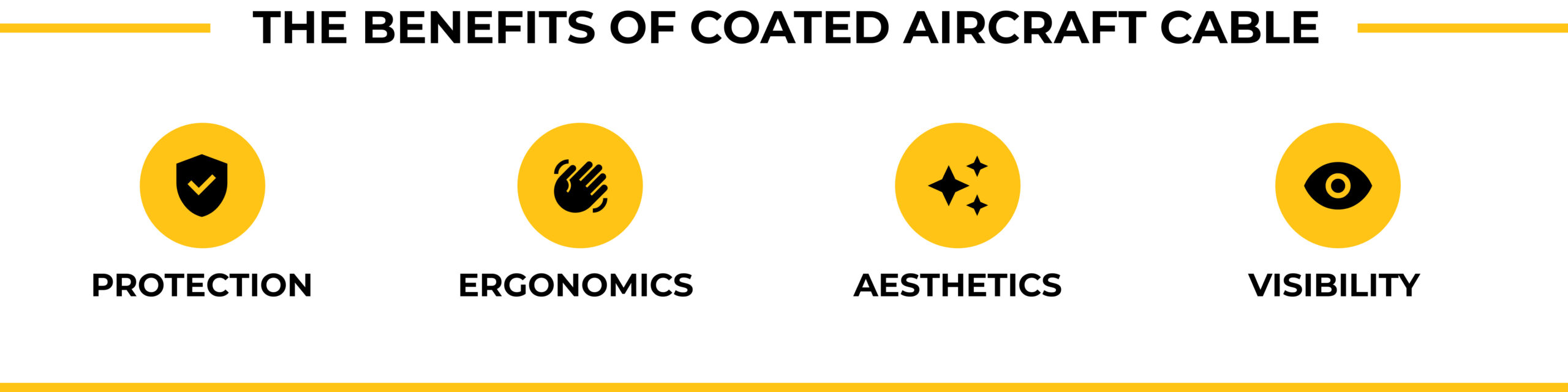
What is Coated Aircraft Cable?
Wire rope is also known as ‘aircraft cable’ due to its extensive use in aerospace applications. This cable is often coated with another material, such as polyvinyl chloride (PVC), nylon, or high-density polyethylene (HDPE). The coating creates a sheath around the cable inside. That sheath helps the strands inside keep their form, while simultaneously altering the outside profile of the cable.
Users require coated aircraft cable for several reasons, including:
Protection
Coating helps to maintain the wire rope inside for longer, protecting it from abrasion and rust. It also prevents water and dust from getting between the strands. In addition, a polymer coating expands the location of use for the cable, with it being capable of being used in wet, dry and saline environments.
Ergonomics
Coated aircraft cable can move easier and cause less abrasion between rope and surface. As a result, coated aircraft cable can significantly improve endurance and equipment function for applications with high friction levels, such as pulleys or sheaves.
Aesthetics
To ensure that critical architectural assemblies fit a building’s style, extrusion coating can come in various colors, materials, and widths. Depending on whether the design calls for the aircraft cable to stand out or fit in different colors can be used for the coating.
Visibility
For safety and awareness, wire rope may be coated with a bright color such as fluorescent red or neon yellow. Wire rope can often be expected to deliver a message about its use without further instruction, so the color used for the coating becomes essential.
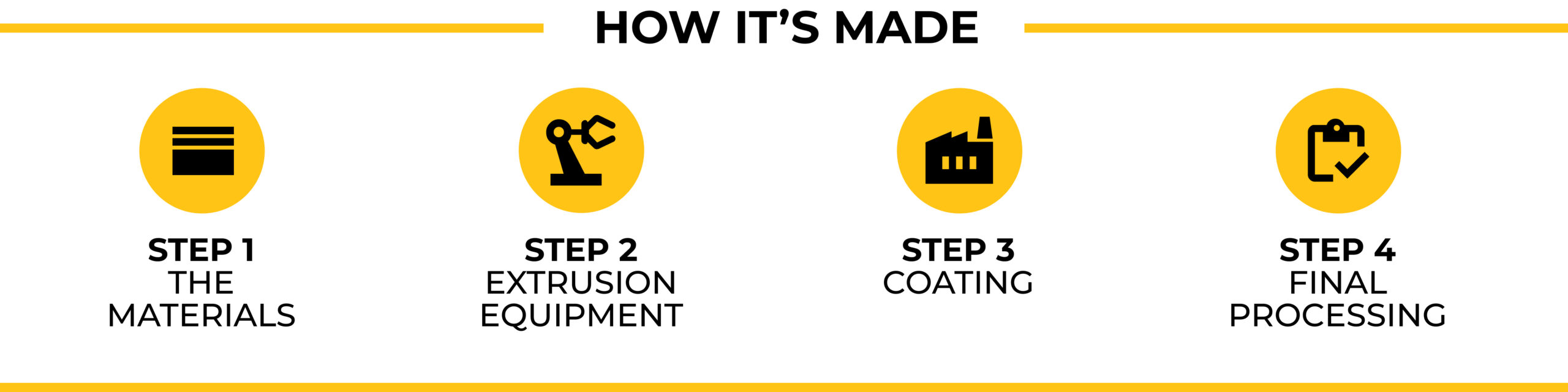
How Extrusion-Coated Aircraft Cable is Created
Step 1 – The Materials: The process of extrusion coating aircraft cable and wire rope begins with the materials which will be used for the coating. This PVC, nylon, or polyethylene (PE) should be new condition/virgin plastic and is transported in the form of resin pellets.
Step 2 – Extrusion Equipment: The resin pellets for the chosen material are loaded into a hopper which feeds the pellets down into the extruder itself. Inside the extruder, the resin pellets are heated until they melt. The bare cable is then reeled out from the pay-off and pulled through this liquefied material to coat it.
Step 3 – Coating: There are a number of settings and parameters to ensure that the coated aircraft cable has a consistent coat that is exactly the thickness the end user requires. The cable travels through pulleys to maintain specific tension and constant line speed. Modern machining can create extremely precise wall thickness or outside diameter (OD) while also ensuring even concentricity along the entire length of the extruded cable.
Step 4 – Final Processing: After being coated, the cable is passed through a cooling trough where the hot plastic is brought down to a temperature where it regains its hardness. After traveling through more pulleys, the now-coated aircraft cable is spooled at the take-up. Coated aircraft cable is generally available by the foot or pre-cut.
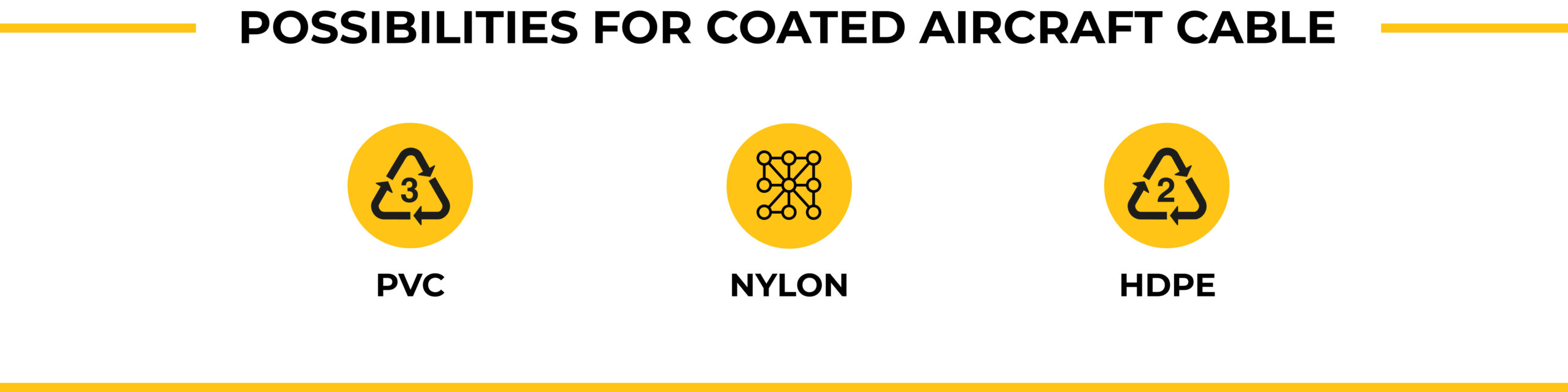
Depending on the application it is destined for, there is a range of variations for coated aircraft cable. To begin with, there are the materials, such as:
PVC
PVC is the most common type of coating for wire rope. It fits most standard coated aircraft cable applications in terms of ergonomics, aesthetics, protection and visibility. It can be coated in assorted colors, including custom colors, to meet application or branding needs. PVC coated cable can also be coiled in a secondary operation.
Nylon
There are two main types of nylon coating, Nylon-6 and Nylon-11. They are generally used for high-friction applications to extend the coated aircraft cable’s lifespan. In addition, nylon has higher temperature ratings than PVC and HDPE and is required for specific applications, such as the military procurement spec MIL-DTL-83420 Type II.
HDPE
This is also generally for very specific applications. HDPE is highly durable and suitable for very low-temperature applications. It is most often used for outdoor applications such as underground cabling.
The color of any coated aircraft cable is also a key element of its potential application. Standard coatings can be translucent or opaque, but a good producer should also be able to provide a variety of other colors as the standard and match specific RAL numbers if required. These can include:
- Red Coated Aircraft Cable – For emergency (e-) stop pulls.
- Yellow and Orange Coated Aircraft Cable – For safety applications.
- High Visibility Colors – For dog leads and ensuring people spot the cable.
- Black Nylon Coated Aircraft Cable – Common fitness cables on gym equipment.
It’s also possible for text to be printed on the cable’s coating, which can significantly benefit cabling that may be found without instruction, such as underground applications.
Coated Aircraft Cable From Lexco
For several reasons, aircraft cable is coated with polymers such as PVC, HDPE, and nylon. First, the coating improves its longevity by keeping out water, salt, and dust and keeping the lubricant between strands. Coated aircraft cable also has ergonomic functions in reducing friction in push-pull applications. At the same time, it also provides an aesthetic and safety function depending on the color it is coated in.
At Lexco, we have coated aircraft cable for all kinds of uses. Depending on your application, they could be a particular blue for blue screen videography, a luminous orange to match a major brand display, specific coloring to match a building façade, or even glow in the dark. We’ve taken a closer look at some interesting uses for our colored extruded cable to draw attention to and enclose a YMCA’s community garden, as well as made-to-order jump ropes to match a university’s cyan team colors.
We take great pride in our products, and all of our coated aircraft cables are inspected throughout the process, both by eye and using laser micrometers, to ensure precise OD measurements. In addition, our large production facility enables us to meet even custom orders quickly. Our extruded cable is available by the foot, reel, pre-cut, or directly as part of your wire rope assembly.
To find out more about ordering your coated aircraft cable from Lexco, you can get a quote here or let our team know your specs here.