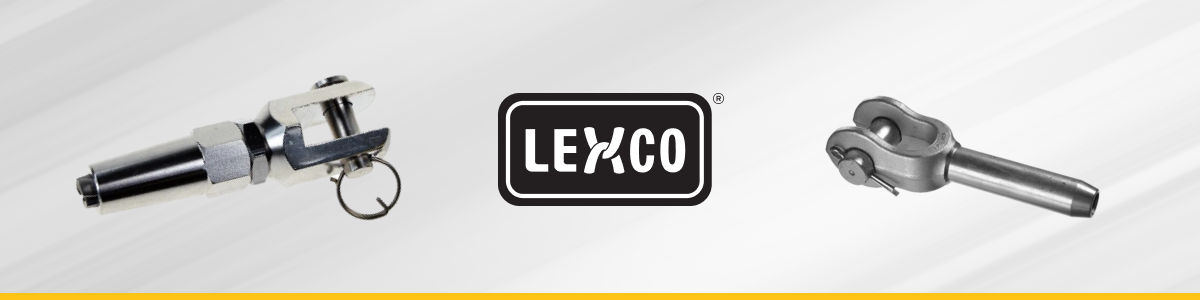
SWAGELESS VS. SWAGED CABLE FITTING: WHICH IS BETTER?
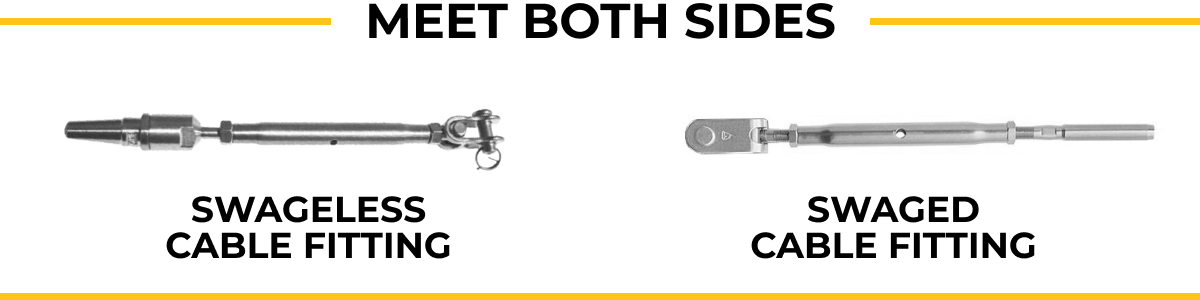
Swaging is a machine tool crimping process carried out to attach wire rope and aircraft cable end fittings. Commonly, swaged endings are hooks, threaded studs, shank balls and eye ends. Loops may also be formed by swaging sleeves, which run the end of the wire back on itself.
Swaging most commonly occurs at the factory, where cable wire fabricators have high-pressure presses that use force to compress the end fittings. However, some fittings can also be added on-site to fit specific purposes using portable crimping tools.
The difference between swaged and swageless cable fittings is that the former uses machine-swaged fittings that support the fitting through compression force. In contrast, swageless cable fittings use a mechanical lock system to hold the fitting in place. Both swaged, and swageless cable fittings have specific advantages and will be deployed in different situations. Here we’ll look closer at swaged and swageless cable fittings and which are best for your application.
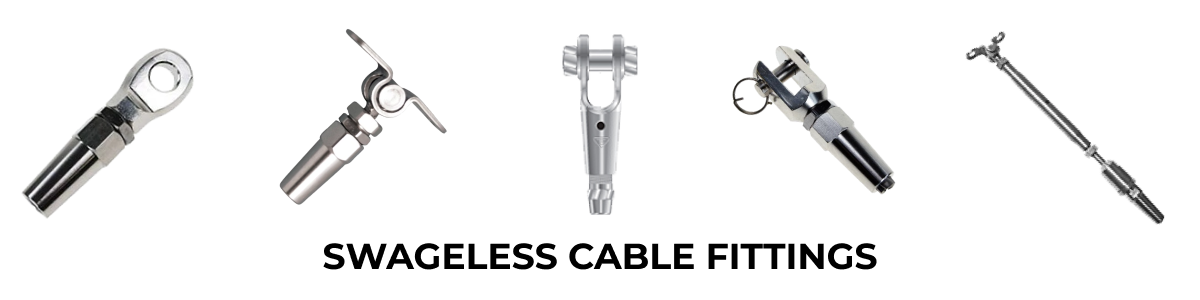
Swageless Cable Fittings: What They Are and What They’re Used For
As swageless cable fittings can be attached in the field, rather than being made to measure at the factory floor, they can allow a technician to install a wire rope assembly to the required dimensions. Then, the technician can run the wire through its final hole, cut and affix a swageless button, stop, or thread end at the optimum tightness for the assembly.
Swageless Warning: Do NOT use swageless wire rope fittings to lift critical loads. Swageless wire rope fittings are primarily used for static loads.
Some examples of swageless cable fittings in use include:
Electroline End Fittings (Swageless)
These are for heavier-duty industrial uses such as rigging, construction, lifeline, tow cables, and various military applications. Electroline examples include hooks, eyes, drum sockets, and coupling fittings. Electroline swageless cable fittings are best deployed as assembly kits to make installation quicker and field adjustment more convenient.
Electroline swageless fittings are typically made in the USA. Some Electroline fittings come in multiple material options, such as zinc-plated steel and stainless steel.
Swageless cable fittings can be applied on-site to fit a specific application where it might not be possible to know precise measurements beforehand. This allows users to adjust the assembly as they wish. When reusing an Electroline swageless fitting, the plug should always be replaced.
Examples of Military Electroline Models:
- NS-4856 Clevis fitting, stainless steel, with sister hook, for 9/16” stainless steel wire rope.
- NS-4843 Clevis fitting, stainless steel, with sister hook, for 7/16” stainless steel wire rope.
- NS-4956 Turnbuckle, closed body, stainless steel, with sister hook, for 9/16” stainless steel wire rope.
- NS-4943 Turnbuckle, closed body, stainless steel, with sister hook, for 7/16” stainless steel wire rope.
- NAK-4850 Clevis fitting, black aluminum, with sister hook, for 1/2″ jacketed black Kevlar rope.
- NAK-4950 Turnbuckle, closed body, black aluminum, with sister hook, for 1/2″ jacketed black Kevlar rope.
Swageless cable fittings are also simple to fit and don’t require any crimping tools or chemical adhesives to stay in place. These cable fittings rely on the mechanics of the fitting, such as springs or tension, to hold the wire fast in place. Always ensure the Electroline plug is compatible with your wire rope or cable strand construction. Notify our salesperson if you have a synthetic rope application.
A block and plug driver is useful for the Electroline swageless installation process. The block allows you to hold the fitting in your vice grip during installation. After the outer wires are installed around the plug, the plug driver helps to seat the plug in the socket sleeve. For some projects, a proof-load may be appropriate to fully seat the plug so it has bottomed in the sleeve.
Kwik Grips (Swageless)
Kwik Grips are swageless cable fittings that can be fastened to a cable end on-site to allow easy installation of lighting or display applications.
For example, at trade show stalls, signage and lighting must be set up with little foreknowledge of dimensions. After adjusting to find the optimum height required, a technician can use Kwik Grips to secure vertically suspended objects in place.
Kwik Locs (Swageless)
These simple, mechanical, swageless cable fittings allow the user to create an eye loop at the end of the wire rope assembly. They are popular for suspending signage, lighting, and HVAC. The user passes the cable through one hole of the Kwik Loc, then forms a loop by bending the end back into a second hole with both being mechanically secured in place.
Kwik lock holds are only rated for use in vertical positions, with angled or pulley uses significantly reducing their weight capacity.
Cable Railing End Fittings (Swageless)
Swageless cable fittings for architectural cables deliver several features. Their robust systems, such as Push-Lock® and Pull-Lock® mechanisms, are available for 1/8” 1×19, 3/16” 1×19 or 1/4” 1×19. The strand where the wire rope is attached using the lock’s internal springs allows several feature-critical endings to be quickly attached in the field, such as eyes, jaws, receivers, studs, or turnbuckles. Cable railings typically have a 300 lbs WLL (working load limit). They also create a different finish and look for public-facing elements.
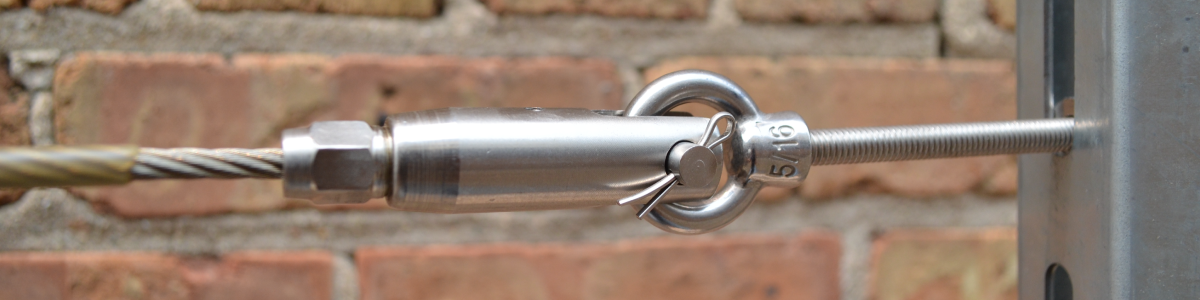
Swaged Cable Fittings: What They Are and What They’re Used For
Swaged cable fittings are most commonly fitted to order at the aircraft cable assembly fabricator’s facility. The user will assess their needs and order swaged eyes, hooks, stops, jaw ends, threaded studs, or whatever they require.
The fabricator will then swage these through industrial presses to compress the fitting’s end over the wire rope, known as crimping. Certain ends can be swaged using hand-crimping tools, but these will not have the same strength as machine-swaged fittings.
Examples of swaged cable fittings in use are visible everywhere that wire rope finds use, such as:
Aerospace
Swaged fittings are used for safety harnesses and lifting slings, both at the harness and pulley ends, in aerospace applications. Eye and ball fittings are also used in aircraft control wires, maintaining perfect tension to allow for precise pilot movement.
Marine
Eye ends, fork ends, threaded terminals, and marine rigging turnbuckles are essential swaged wire rope fittings that allow both professional and recreational mariners to hold wires and equipment in place. Swaged fittings and cable assemblies for marine usage generally come in corrosion-resistant stainless steel to keep the assembly functional in freshwater and saltwater environments and chlorinated pools. Some marine turnbuckles are available in a swageless option.
Fitness
In gyms and at home, fitness cable is held in place by swaged cable endings which function against a high degree of resistance, keeping users safe and ensuring machines work as intended. The most common swaged fittings in fitness settings are ball ends, eye ends, and thimble loops.
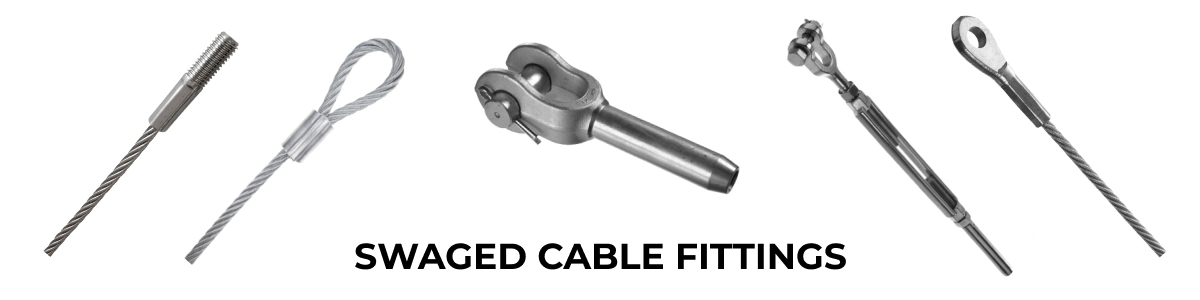
Swageless vs Swaged Cable, Summarized
Swaging is the process by which fittings are attached to aircraft cable and wire rope. The fitting is most commonly crimped using machine presses on the factory floor, with the user ordering the specific ending. Swageless cable fittings are not machine or hand crimped; instead, make use of mechanical processes, such as springs or tension, to lock the cable in place.
Swageless cable fittings are less common but have advantages, such as being adjustable on-site and relatively quick to fit.
Threaded studs, forks, and eyes come in both swaged and swageless options. Button stops, plain balls, and shank balls are typically only available in swage type. Loops are swaged with sleeves. Typically, field-installed loops are clamped via wire rope clips. Another swageless option is called a Safeline Clamp.
Plastic coatings should be stripped at the termination to optimize end fitting strength. Exercise caution when using powder-coated cable; the paint can diminish holding strength, especially with swageless end fittings. End fittings are generally designed for linear applications. Angular loads should be avoided whenever possible. To test assembly strength, proof-loading and pull-testing are recommended.
Swageless cable fittings are either field-installed or factory installed. Swaged end fittings are typically only factory installed, with the exception of some portable crimp tool applications. Proof-loading and pull-testing are generally more practical in a controlled environment at the assembly fabricator’s factory.
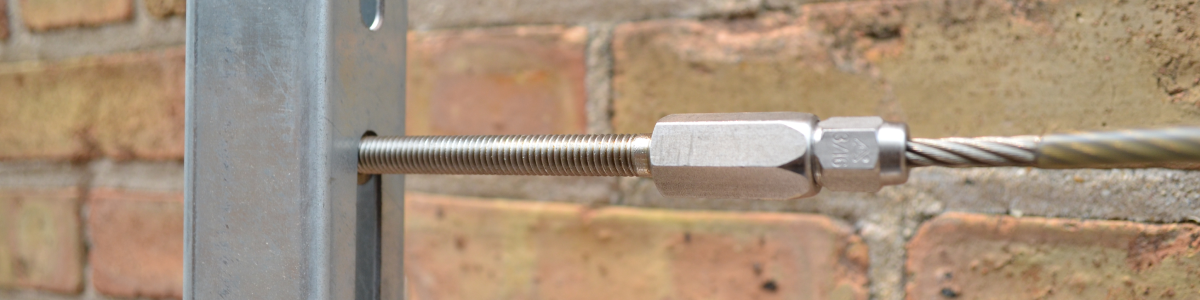
Conclusion
For all your needs regarding swaged and swageless cable fittings, you can view Lexco® Cable’s extensive gallery. Want an expert opinion from one of Lexco’s experts? Talk to our team here about your specifications.
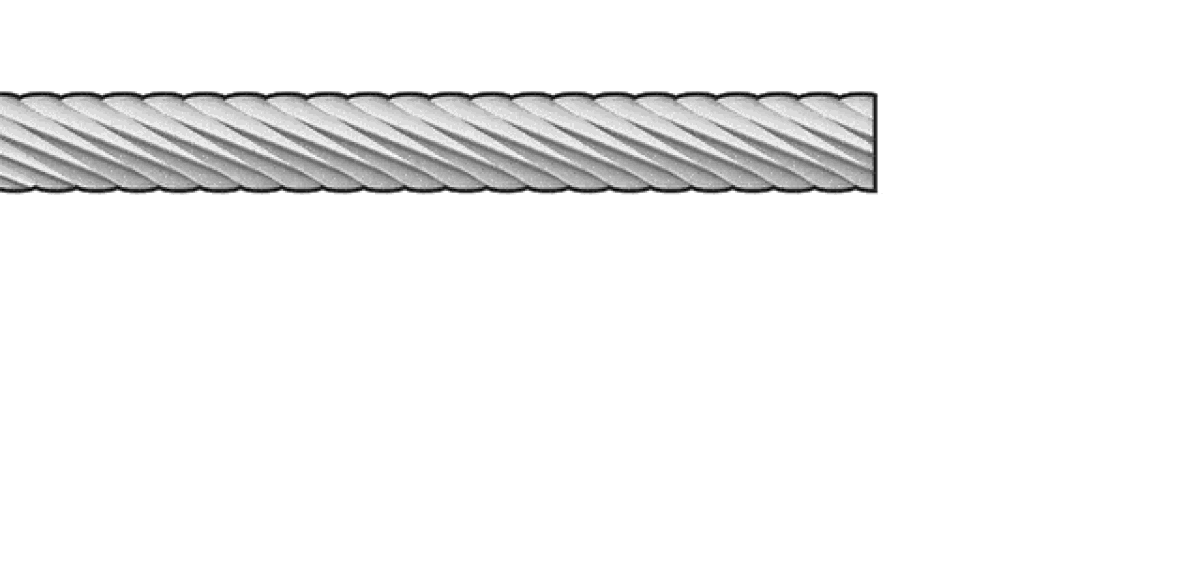
PRODUCTS MENTIONED IN THIS BLOG