PROOF-LOADING ANDPULL-TESTING CAPABILITIES
Lexco® Cable is an industry-leading wire rope assembly manufacturer offering extensive proof-loading and pull-testing services to ensure safety and quality in our wire rope assemblies.
PROOF-LOADING AND PULL-TESTING CAPABILITIES
Lexco® Cable is an industry-leading wire rope assembly manufacturer offering extensive proof-loading and pull-testing services to ensure safety and quality in our wire rope assemblies.
TESTING THE LIMITS
Proof-loading and pull-testing ensure that our wire rope assemblies meet your safety, quality, and application requirements. Routine proof-loading is recommended for critical load applications and destructive pull-testing is recommended for any load-bearing cable to qualify its design. Proof-loading and pull-testing can be a vital part of the quality control process, and our equipment is calibrated in accordance with UCC Procedure 100 and meets the requirements of ASTM E4-16. We can provide you with pull-testing and proof-loading up to 180,000 lbs.
A proof-load test is a controlled, measured application of force over a specified time period to a given piece of rigging equipment. The results of a proof-load can help discover defective parts by finding subtle issues that some visual and dimensional inspections can miss. If the part fails a proof-load test prematurely it can be further investigated as appropriate. Assemblies that pass proof-load testing provide extra quality assurance.
Proof-loading is commonly required when the assembly will play a critical role in an application. Such critical applications include using the wire rope assembly for lifting, overhead safety, structural support, aerospace, and military use cases, or situations requiring a MIL-DTL-6117 or MIL-DTL-5688 certification. Applications that are commonly proof-load tested include critical lifting, where the load may be overhead or of high volume, and structural assemblies, such as suspension cables on a bridge. After a proof-load is done, the assembly is inspected for defects, and, at your request, we can apply a proof-load tag to the assembly and proof-load documentation.
For commercial-grade assemblies with terminations that hold to the wire rope’s nominal breaking strength, a nominal break of 40% or 50% is common. If the proof-load is in compliance with MIL-DTL-6117 or MIL-DTL-5688, then the test load shall be 60% of the terminal break strength or 60% of the wire rope nominal break strength, whichever is lower. It is not recommended to proof-load above 60% of an assembly’s nominal break strength to avoid fatiguing the assembly.
A pull-test is when one end of the cable is fixed while the other end is attached to a movement force, such as a hydraulic cylinder, typically along a linear axis. Pull-tests create a specific force over a set period of time to test the cable under set force and time parameters. As demonstrated in this pull-testing video, pull-tests are designed to test tensile strength – the resistance of a material to breaking under tension. The results of a pull-test will indicate the break strength of a cable assembly based on a gradual linear pull.
Pull-testing can be destructive or non-destructive. Destructive pull-tests are used for process setups, while non-destructive testing is used for the final quality control testing. Our pull-testing machines are on a regular calibration schedule to maintain accuracy and ensure the safety and reliability of your assembly. The typical proof-load and destructive pull-test we perform are with a gradual and linear applied load. For applications involving a shock load, a higher safety factor is required. Whereas a general rigging safety is 5:1, a critical or shock load safety factor may need to be 10:1.
We can also perform pre-stressing (aka pre-stretching) on structural cables to reduce constructional stretch. Pre-stressing subjects the wire rope to three cycles of tensile loading at 40 percent of its nominal strength for 5 minutes and returns the tensile load to 5 percent of the nominal strength between cycles. After the last cycle, the tensile load is completely released. When specified, ropes may be pre-stressed using either a process of static or dynamic loading. Commonly pre-stressed applications include suspension bridge structural cables, barrier cables for parking garages, elevator cables, and cables used in seismic bracing. Pre-stressed loads shall not exceed 55% of the minimum breaking force for the rope, and stranded ropes are not pre-stressed unless otherwise specified.
Our team has been conducting proof-load tests and pull-tests for decades, but only you can determine the necessity of a proof-load or pull-test for your application. Lexco will only proof-load or pull-test if specified in your RFQ, PO, or drawing. If you are uncertain whether your application requires proof-loading or pull-testing, our team is here to help. We can assist you in determining how your working load limit intersects with your assembly’s strength. Once determined, you can verify whether a proof-load or pull-test is necessary, appropriate for a single piece, needed for a percentage of your assemblies, or required for every piece. When you need to ensure the reliability of your assembly and the safety of your project, look no further than Lexco.
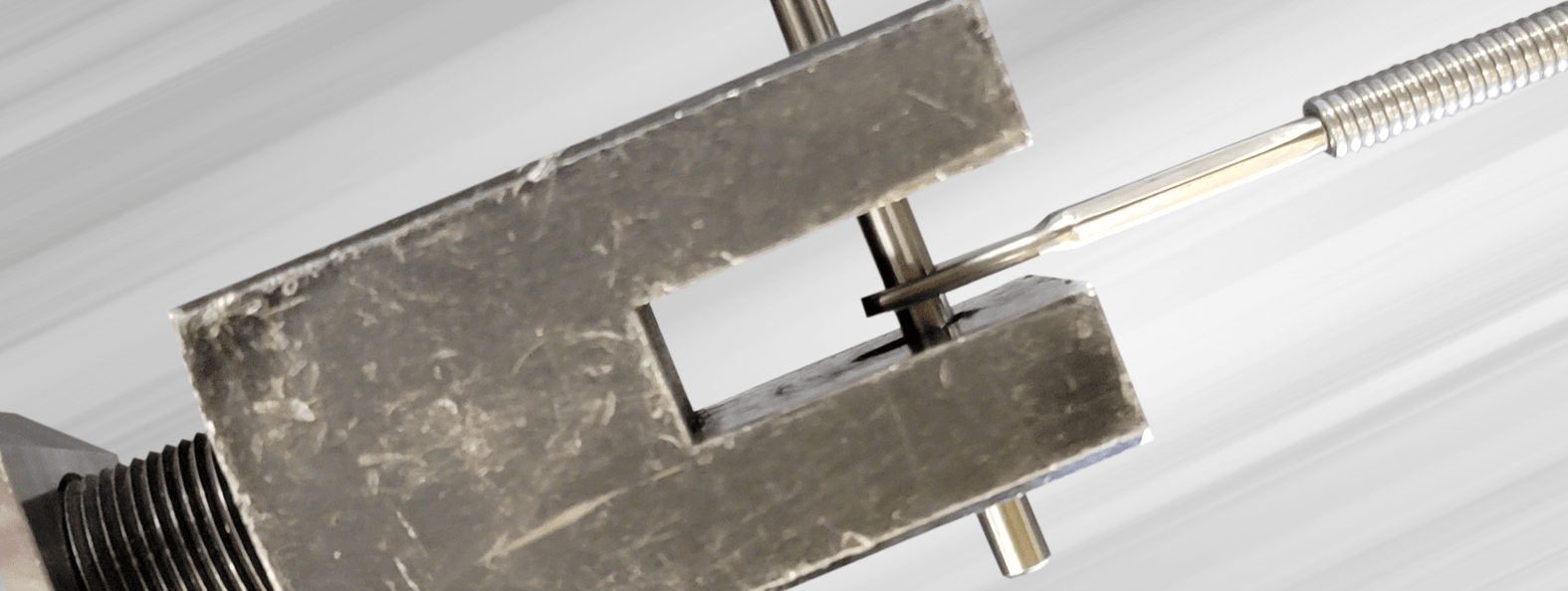
Tests We
Perform
Our first-class proof-loading and pull-testing equipment can cover a wide variety of your safety and project requirements. If you’re uncertain if you need a proof-load or pull-test, or to learn more about which test is right for your assembly, contact us directly. Some common proof-load tests and pull-tests we perform are:
- Pull-testing and Proof-loading up to 180,000 lbs
- MIL-DTL-6117 Proof-loading
- MIL-DTL-5688 Proof-loading
- Commercial Grade Proof-loading
- Destructive Pull-testing
- Non-destructive Pull-testing
- Pre-stressing/Pre-stretching
- And More
Who We
Work With
Lexco’s proof-loading and pull-testing capabilities are ideal for ensuring your assembly safely meets or exceeds the requirements of your project. Among the partners and industries we are proud to support are: